We regularly conduct measurement and optimisation projects for industrial plants (e.g. rotary kiln plants in the cement industry) and have been familiar with the requirements of industrial practice for many years. Within the framework of research projects, we systematically work to improve our understanding of process technology and continuously develop our methods and procedures. As a reliable and independent partner we can offer our assistance with complex interdisciplinary projects as well. We are happy to advise you and work together to find a tailor-made solution for your problem. This also includes performing Technical Reviews.
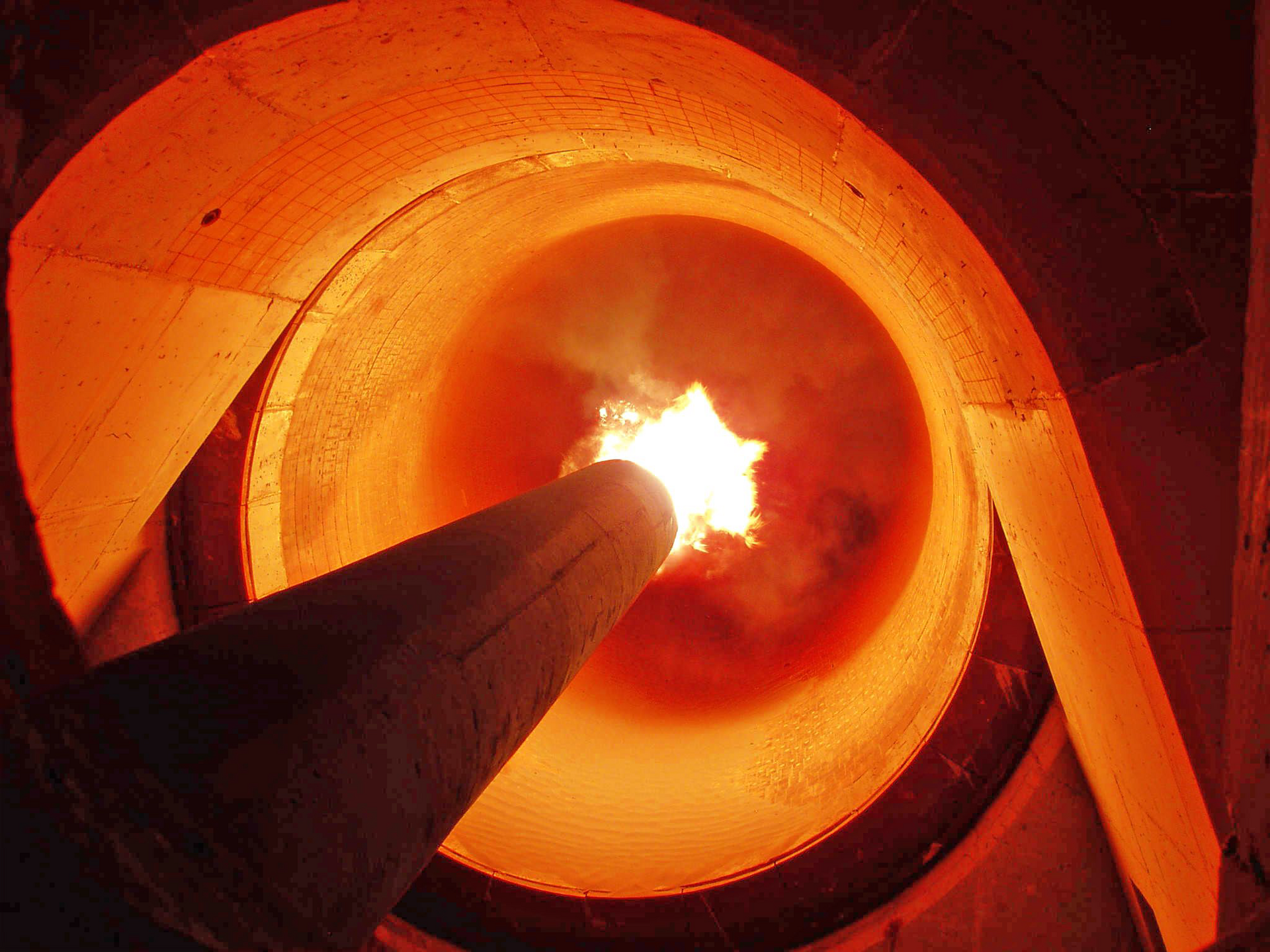
Thermal process technology
We offer a comprehensive service portfolio covering the entire field of thermal process technology. We can advise you on every aspect of process optimisation, product quality, energy efficiency and the use of alternative fuels and raw materials. In addition we also conduct measurements in high-temperature processes as well as performing process technology modelling. Our expert technicians are trained to take process measurements. Our experienced engineers have many years of practical knowledge and keep up with the results of the latest research. The work of our experts is mainly focused on customers from the cement industry world wide, as well as e.g. aggregate and lime industry.
Our methods
a) Process optimisation
- Technical analysis of the clinker burning process/the entire rotary kiln plant
- Weak point analysis
- Chemical and physical analysis of all materials, checking and optimisation of clinker and cement quality
- Optimisation of kiln plant operation
- Diagnosis and consultation in the event of incrustation build-up
b) Optimisation of product quality
- Chemical/mineralogical recording and assessment
- In-depth study of the influence of burning and cooling conditions as well as of raw materials and fuels on product properties
c) Enhancement of energy efficiency
- Determination and analysis of energy demand taking into account plant-specific production processes
- Production of complete and sequential energy balances, benchmarking with respect to the VDZ database and BAT values
- Identification and quantification of savings potential
- Consideration of CO2 abatement measures
- Determination of potential for cost savings
d) Measurements in high-temperature processes
- Measurement of gas composition, dust content and temperatures in the range up to 2000 °C and dust content up to 500 g/Nm³
- Sampling of solids and liquids
e) Alternative fuels and alternative raw materials
- Conducting of combustion-technology studies on the use of alternative fuels and raw materials
- Effects and material cycles (sulphur, chlorine, alkalis)
- Analysis of alternative fuels
- Thermographic flame investigation using a mobile thermographic system
- Production of proposals for optimisation of the burner setting and the use of alternatives
f) Process technology modelling
- Simulation studies with practice-oriented process model
- Assessment and design of plant conversions
- Assessment of planned operational activities before implementation
- Determination of data not measured (e.g. kiln profiles with regard to temperatures, gas composition, chemical/mineralogical material transformation etc.)
- Effect of operational changes and process-modifications on clinker quality
Your benefits
- Sustained optimisation of the production process
- Maintenance and enhancement of cost-effectiveness and competitiveness
- Consultation taking account of the latest developments
- Internationally experienced plant specialists to diagnose weak points and develop solutions
- Specific energy efficiency analyses for the identification of potential opportunities for savings in the production process
- Benchmarking of data gathered by comparison with the VDZ database and BAT (best available techniques)
- Accredited and quality-assured measurement procedures
- Results are presented in comprehensible form in a report
- Integrated study of kiln operation, product quality and environmental performance taking into account economic aspects
- Incorporation of the latest findings from research and technology
- Simulation studies with practice-oriented process model
- The VDZ process model can be used as a substitute for tests on the kiln system which could result in damage